Crucial Considerations for Troubleshooting and Fixing Your Product Packaging Equipment
When addressing the complexities of troubleshooting and repairing your product packaging machine, numerous crucial variables have to be considered to make certain both efficiency and safety. What other essential elements could be the trick to enhancing your device's reliability?
Comprehending Typical Problems
Determining common issues in packaging devices is vital for preserving functional performance and decreasing downtime. Packaging devices, essential to production lines, can encounter a selection of issues that hinder their performance. One prevalent problem is mechanical breakdown, typically resulting from wear and tear on elements such as belts and equipments, which can bring about irregular product packaging top quality.
One more usual issue is misalignment, where the product packaging materials might not align properly, triggering jams or inappropriate sealing. This misalignment can originate from improper configuration or modifications in product specifications. Furthermore, electric failures, such as defective sensing units or control systems, can interfere with the maker's automated procedures, resulting in manufacturing hold-ups.
Operators may also experience challenges with software application glitches, which can impact device programming and functionality. In addition, poor maintenance practices commonly contribute to these issues, emphasizing the demand for regular examinations and prompt service interventions. By understanding these typical problems, drivers can implement proactive actions to ensure peak efficiency, thereby minimizing costly downtimes and enhancing overall productivity in packaging operations.

Analysis Tools and Methods
Efficient troubleshooting of packaging devices relies heavily on a range of analysis devices and techniques that help with the identification of underlying problems - packaging machine repair service. Among the main devices is making use of software program diagnostic programs, which can keep track of maker efficiency, assess error codes, and offer real-time information analytics. These programs allow technicians to pinpoint certain malfunctions promptly, considerably minimizing downtime
In enhancement to software program oscilloscopes, multimeters and solutions are important for electric diagnostics. Multimeters can measure voltage, current, and resistance, assisting to recognize electric mistakes in circuits. Oscilloscopes, on the various other hand, provide visualization of electric signals, making it easier to detect abnormalities in waveforms.
Mechanical concerns can be detected making use of vibration evaluation devices and thermal imaging cameras. Resonance analysis enables the discovery of inequalities or misalignments in equipment, while thermal imaging assists recognize overheating parts that might lead to mechanical failing.
Last but not least, aesthetic evaluations, incorporated with basic lists, stay invaluable for standard troubleshooting. This detailed method to diagnostics ensures that professionals can properly deal with a wide variety of concerns, consequently boosting the dependability and performance of packaging devices.
Security Procedures to Follow
Just how can packaging device drivers guarantee a safe workplace while troubleshooting? The execution of rigorous security protocols is important. Operators must start by separating the machine from its source of power before launching any type of troubleshooting procedures. Lockout/tagout (LOTO) techniques need to be implemented to stop unintentional re-energization throughout upkeep.
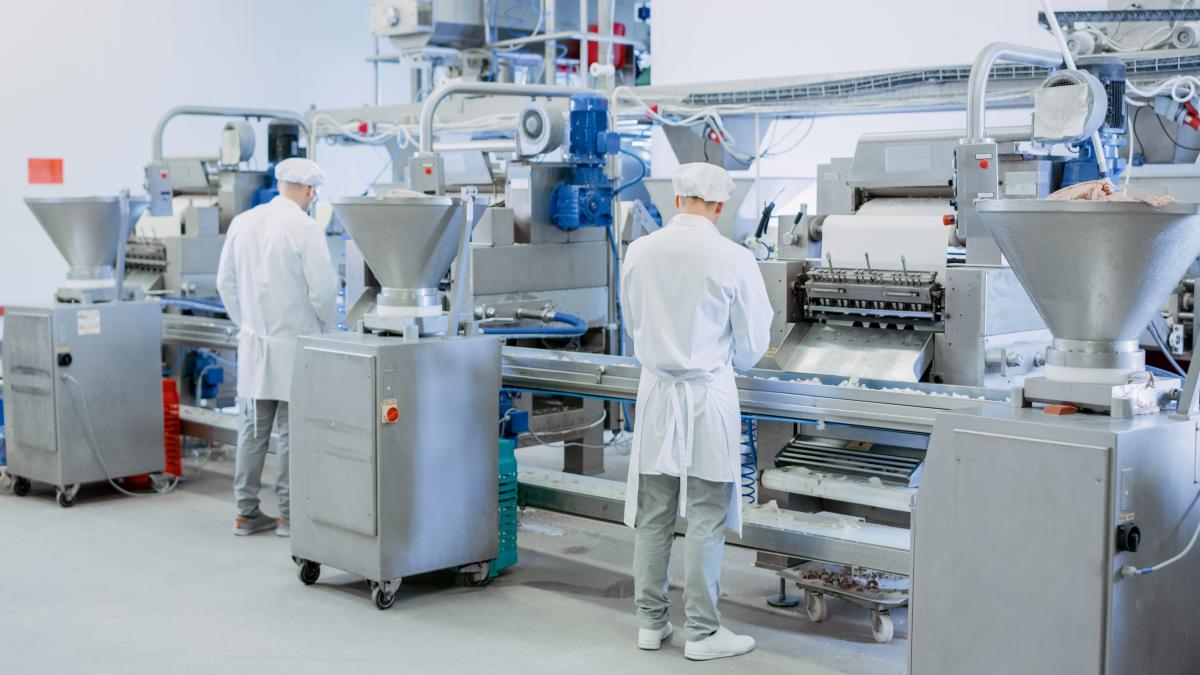
Operators should likewise familiarize themselves with the device's security features, such as emergency stop buttons and safety guards, verifying that they are functional before starting any kind of analysis job. packaging machine repair service. It is vital to communicate with group members, making sure all workers are mindful of the recurring troubleshooting tasks
Last but not least, operators need to document all treatments and findings, giving a clear document in case of future problems. By sticking to these security protocols, packaging device operators can produce a much safer environment, lessening threats while properly troubleshooting and fixing machinery.
Components Substitute Standards
When it comes to preserving packaging devices, recognizing parts replacement standards is vital for ensuring optimum performance and longevity. Consistently assessing damage on equipment parts is critical, as prompt replacements can stop a lot more substantial damages and expensive downtime.
To start with, constantly refer to the supplier's requirements for recommended substitute intervals and part compatibility. It is vital to use OEM (Original Tools Producer) components to assure that substitutes fulfill the called for high quality and efficiency standards.
Before beginning any type of replacement, guarantee the maker is powered down and correctly locked out to stop unexpected activation. Paper the problem of the changed parts and the date of substitute, as this will aid in tracking upkeep trends gradually.
In addition, assess the bordering components for indications of wear or potential concerns that may emerge from the replacement. This all natural approach can reduce future troubles and boost operational effectiveness.
Lastly, after replacing any parts, conduct extensive testing to make sure that the equipment is operating appropriately and that the new parts are integrated perfectly. Following these standards will certainly not only prolong the life of your packaging maker yet also boost total productivity.
Maintenance Finest Practices
Constant upkeep methods are vital for taking address full advantage of the performance and life expectancy of product packaging makers. Developing a thorough upkeep schedule is the very first step toward ensuring ideal efficiency. This schedule needs to include daily, weekly, and monthly tasks customized to the particular device and its operational needs.
Daily checks must concentrate on i loved this necessary parts such as belts, seals, and sensing units, ensuring they are tidy and functioning appropriately. Weekly upkeep could entail evaluating lubrication degrees and tightening up loosened fittings, while monthly tasks should include more extensive assessments, such as placement checks and software updates.
Using a list can simplify these processes, ensuring no critical jobs are forgotten. Furthermore, preserving accurate documents of upkeep activities assists recognize reoccuring issues and educates future approaches.
Educating team on proper use and handling can significantly lower deterioration, avoiding unneeded failures. Spending in top notch components and lubricants can improve equipment efficiency and integrity.
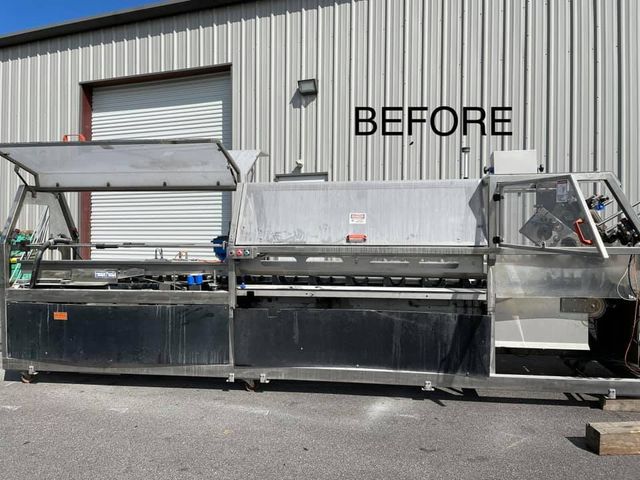
Verdict
To conclude, effective repairing and repair service of packaging equipments require a structured strategy including safety and security methods, making use of suitable diagnostic devices, and adherence to maintenance ideal practices. Prompt components and routine assessments substitute with OEM elements play an essential role in sustaining machine efficiency and integrity. Careful documents of procedures and searchings for contributes to a much deeper understanding of persisting concerns, eventually enhancing functional performance and lowering the probability of future breakdowns.
When dealing with the intricacies of troubleshooting and fixing your packaging machine, a number of vital factors need to be considered to make sure both performance and safety.Identifying typical problems in packaging devices is necessary for keeping functional performance and decreasing downtime.Reliable troubleshooting of product packaging machines relies heavily on a variety of analysis devices and strategies that assist in the identification of underlying problems.Just how can packaging device operators make sure a risk-free working environment while troubleshooting?In conclusion, reliable repairing and fixing of product packaging equipments necessitate an organized method including safety methods, the usage of ideal diagnostic tools, and adherence to upkeep ideal methods.